Process Pump and Gearbox Repair Solutions by SunSource
With over 30 years of industry expertise, SunSource has established itself as a trusted leader in process pump and gearbox repair. Specializing in a wide range of equipment, we are capable of repairing:Â
- Horizontal and vertical ANSI pumps
- API pumps
- Centrifugal pumps
- Vertical turbine pumps
- Positive displacement pumpsÂ
- Gearboxes
With our broad range of knowledge and experience, we are the go-to partner for industries seeking reliable and efficient repair solutions.
Comprehensive Pump and Gearbox Repair Process
At Sunsource, we follow a detailed step by step repair process to restore your pump to peak performance. The repair process consists of the following steps:
- Receiving and Processing:
- When a pump is received, it will be logged into our Trend data management system with customer information, urgency level, and tracking number.
- Technician Assignment:
- Once the pump has been entered into the system, Â it will then be assigned to a skilled technician who is supplied with a folder containing all relevant documents for that specific repair.
- Teardown and Evaluation:
- Once the unit has been assigned, the technician will then begin disassembling, cleaning, and inspecting the pump. During this process, the technician will document the as found condition of the pump and determine what replacement parts or modifications will be required.
- As applicable, a failure analysis will also be performed to determine the root cause of failure on the unit. When the root cause is identified, we will use our expertise to determine what the best course of action is to mitigate the same failure from occurring again.Â
- Repair Quoting:
- Once the unit has been disassembled, a comprehensive repair estimate will be prepared. This repair estimate will cover parts, labor, a timeline for completion and a detailed breakdown on what was found and what is to be repaired.
- Repair Execution:
- Once the quote has been approved by the customer, the repair process will begin. Each pump is meticulously rebuilt to meet first-class API or industry standards, ensuring it performs like new or better.
- Testing and Quality Assurance:
- After the pump is assembled, the pump will undergo various testing to ensure it meets or exceeds industry standards. All tests will be documented for reference and are made available to the customer.
- Shipping and Delivery:
- After passing testing and quality assurance, the pump will be painted and prepared for shipment. Upon completion, a detailed repair report will be supplied documenting the repair process from beginning to end.
The Sunsource Advantage in Process Pump and Gearbox Repairs
Choosing SunSource means benefiting from our proven expertise and customer-first approach:
- Skilled Technicians: Experienced technicians ensure accurate and reliable repairsÂ
- 12 Month Warranty: We stand by our repairs with a comprehensive warranty covering materials and workmanship
- Emergency Repair Services: Our teams can respond to emergency repairs rapidly and minimize downtime
- Nationwide Repair Network: With multiple process pump repair facilities across United States we are able to provide fast convenient service
- Detailed Communication: During the repair process you will routinely receive updates on the repair
In Housing Testing Capabilities
At our SunSource  facilities, we also have the capability to perform testing on your process pumps ensuring they perform at their best during operation. Some of these testing capabilities include:
- Air leak testing
- Nitrogen leaking testing
- Rotor balancing
Experts in Process Pump and Gearbox RepairÂ
At SunSource, we are industry leaders in pump repair, renowned for our expertise in restoring performance and reliability to many industries. With a proven track record of delivering successful repairs, our team combines decades of hands-on experience with proven solutions to meet the most demanding operational challenges. Whether you require routine repairs, tailored retrofits, or comprehensive system enhancements, we are committed to optimizing your equipment’s performance and extending the service life of your process pumps and gearboxes. We will do our best to ensure your equipment is more reliable and cost effective throughout its lifetime. At SunSource, we don’t just fix your equipment, we engineer reliability into them, providing you with a solution that will keep your operation running smoothly for years to come.
Brands We Service:
With our extensive experience repairing rotating equipment, we repair equipment from industries leading brands including:
Pumps:Â
- Goulds
- Pulsafeeder
- Roper
- Magnatex
- Flowserve
- Seepex
- Pacific
- Liquiflo
- Sulzer
- Moyno
- Ingersol Rand
- Franklin Electric
- Ruhrpumpen
- Sandpiper
- Allweiler
- Oberdorfer
- Clyde Union
- Viking
- Gorman Rupp
- Trillium
- National Pump
- ARO
- Durco
- AMT
- Worthington
- Gunard
- Yamada
- Hidrostal
- Nash
- Haynes
- Roto-Jet
- WildenÂ
- IMO
Gearboxes:Â
- SPX Lightnin
- SPX Philadelphia
- Marley
- Falk
- Westech
- Amarillo
- Sumitomo
- Chemineer
Submit request for pricing on RFQ products.
Our sales team will be in touch to provide you a quote.
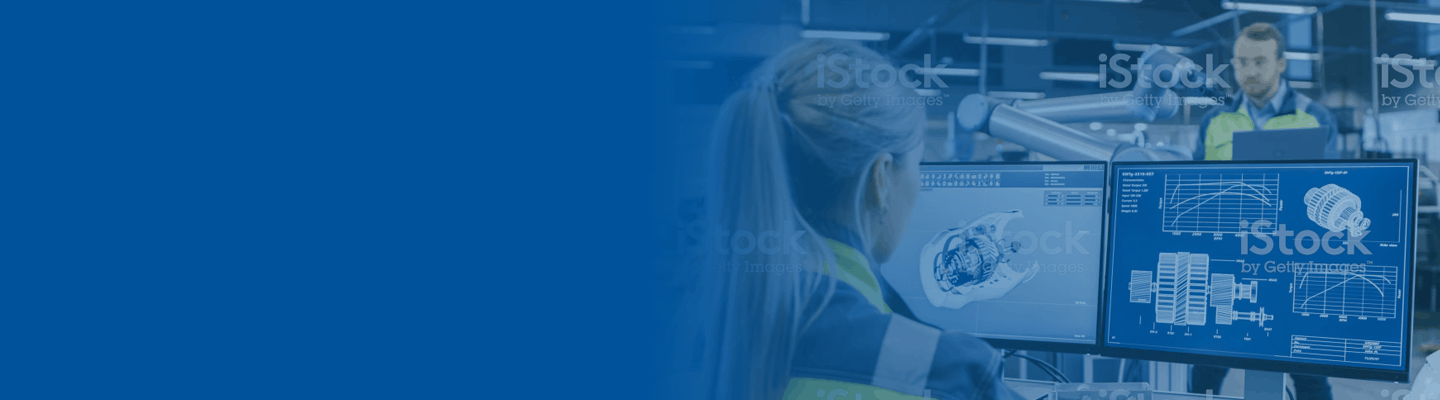
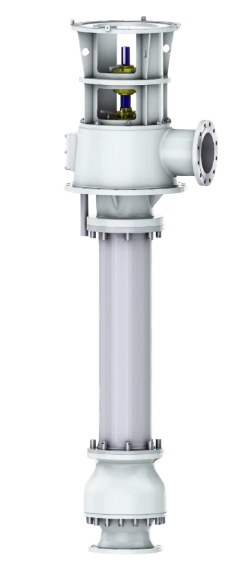